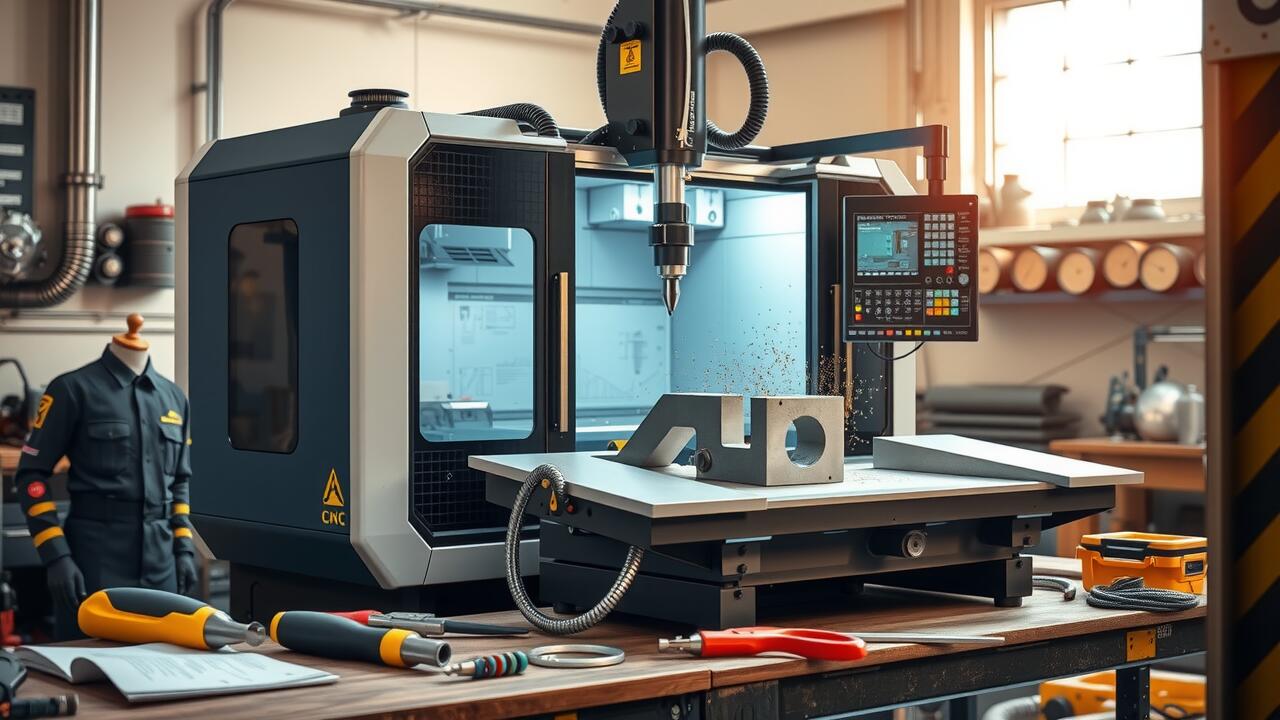
Key Takeaways
- Grasping CNC Machining Fundamentals
- The Process of CNC Machining Explained
- Varieties of CNC Machining Techniques
- Tailored CNC Machining Solutions
- Equipment Utilized in CNC Machining
- Materials Used in CNC Machining Applications
- Services Offered in CNC Machining
- Role of CNC Machining in Production
- Enhancements in CNC Machining Efficiency
Understanding CNC Machining
CNC machining, or computer numerical control machining, revolutionizes the manufacturing process by utilizing advanced technology to automate machining tasks. CNC machining centers are equipped with sophisticated CNC machine tools that enhance precision and efficiency. These centers perform various machining operations, including CNC milling and turning, using specialized machining tools designed for intricate tasks. CNC milling machines, a vital component of this process, enable the creation of complex parts with high accuracy. The integration of technology in CNC machining allows manufacturers to achieve consistent quality and significant time savings, laying the foundation for modern manufacturing practices.
What is CNC Machining?
CNC machining refers to a computerized process that utilizes precision tools to create intricate components and parts. This technique involves various methods such as multiaxis machining, spark machining, and electrochemical machining, which allow for the fabrication of highly detailed designs. CNC machines operate using a variety of CNC equipment that translates computer-generated designs into physical products, achieving accuracy that manual machining cannot replicate.
The versatility of CNC machinery enables it to work with a wide array of materials, accommodating projects ranging from simple to complex geometries. CNC machined parts are common in numerous industries, including aerospace, automotive, and medical sectors, due to their reliability and consistency. As technology advances, CNC machines continue to evolve, offering manufacturers innovative solutions for efficient production and enhanced quality control.
Benefits of CNC Machining
CNC machining offers precise and consistent results, making it an excellent choice for various manufacturing applications. Techniques such as swiss screw machining and electric-discharge machining play integral roles in enhancing production efficiency. Skilled machinists utilize CNC machines to achieve intricate designs that traditional methods may struggle to replicate. The ability to produce multiple identical components rapidly is a significant advantage, particularly in industries requiring high-volume output.
Cost-effectiveness is another key benefit of CNC machining, as it often reduces labor costs and minimizes material waste. CNC milled parts can be produced with exceptional accuracy, resulting in fewer defects and decreased post-processing requirements. The versatility of electrical discharge machining (EDM) allows for the machining of complex shapes and hard materials, further enhancing manufacturing capabilities. By adopting CNC machining, businesses can streamline their operations while maintaining high standards of quality and precision.
The CNC Machining Process
CNC machining involves a series of precise operations performed by highly skilled machinists using advanced equipment. Key methods include CNC milling and CNC turning, which utilize CNC mill and CNC lathe machines to create intricate parts from various materials. Abrasive jet machining represents another innovative technique within the CNC machining realm, ensuring high levels of machinability for complex designs. The process encompasses several critical steps, from initial programming to the final inspection of the product, allowing for efficient production and consistency across different applications. Understanding these elements is essential for effectively utilizing CNC machining in modern manufacturing practices.
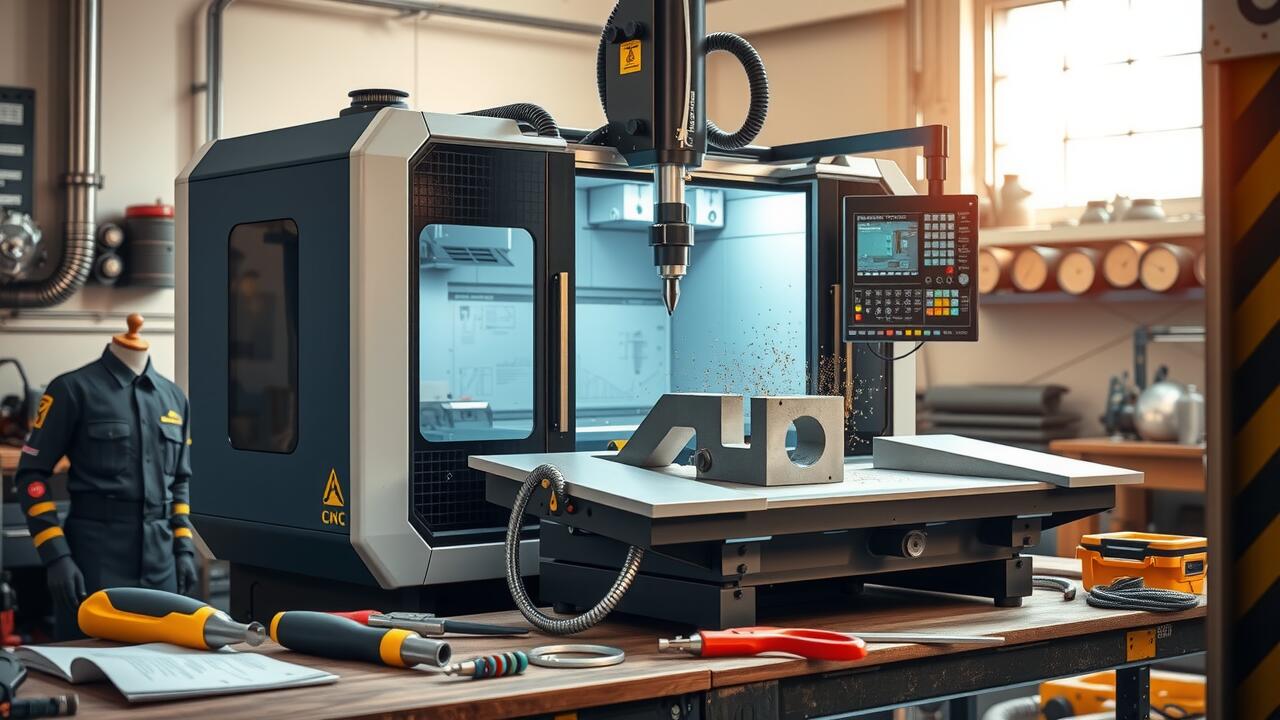
Overview of the CNC Machining Process
CNC machining is a process that utilizes advanced technology to automate the control of machine tools through a computer. This method encompasses various techniques, including cnc lathe machine operations, cnc plunge milling, and milling machines. Each CNC machine is operated by a CNC controller, which interprets instructions from CNC programming to achieve precise manufacturing results. By employing machine tooling and robotics, CNC machining enhances efficiency and ensures high levels of accuracy across diverse applications.
The CNC machining process begins with designing a detailed blueprint that is translated into code for the CNC system. This code directs the machine, guiding components such as a cnc lathe machine or milling machine to perform specific tasks. This intricate interplay between CNC programming and machine tooling allows for consistent replication of parts and products. As manufacturers increasingly rely on these automated systems, the implications of CNC machining on production speed, quality, and cost-effectiveness continue to reshape the industry landscape.
Key Steps in CNC Machining
CNC machining involves several key steps that ensure precision and accuracy throughout the fabrication process. The initial phase typically includes designing a detailed CAD model, which serves as a blueprint for the machine tools. The transfer of this digital design to the computer numerical control (CNC) system directs the milling cutter and other machine tools to execute specific tasks. This transition from design to execution is critical for achieving the desired specifications in the final product.
Following the design phase, the next step is the setup of milling machines, where the material is firmly secured for processing. Operators input the necessary parameters into the CNC system, ensuring that the milling cutter is aligned properly. The machine then follows the programmed instructions, which can include chemical milling for specific materials, to produce parts with intricate designs. This systematic approach exemplifies the efficiency and effectiveness of CNC machining in modern fabrication.
Types of CNC Machining
CNC machining encompasses various specialized processes that cater to diverse manufacturing needs. Among these, CNC milling and CNC turning stand out as two predominant methods employed in cnc machine shops. CNC milling involves removing material from a workpiece using rotary cutters, allowing for intricate designs and precise detailing in custom CNC machining projects. Conversely, CNC turning focuses on rotating the workpiece against a cutting tool, enabling the efficient shaping of cylindrical components. Both methods rely on advanced CNC machining equipment to produce high-quality CNC machining parts with exacting tolerances. The term CNC machining encapsulates these techniques, highlighting their significance in the realm of mechanical CNC machining and overall manufacturing efficiency.
CNC Milling
CNC milling is a vital aspect of the CNC machining process, focusing on removing material from a workpiece to achieve desired shapes and sizes. This method primarily utilizes CNC machining cutting tools, which are precisely controlled by a computer, enhancing accuracy and reducing human error. With the introduction of instant CNC machining and online CNC machining services, businesses can have quicker turnaround times and greater flexibility in their manufacturing processes. CNC milling is widely employed across various sectors within the CNC machining industry, solidifying its importance.
The versatility of CNC milling allows for a broad range of CNC machining materials to be utilized, including metals and plastics. Start-up CNC machining companies often rely on this technique due to its efficiency and cost-effectiveness. By leveraging CNC machining services that specialize in milling, manufacturers can produce complex components with high precision. This allows for innovation and adaptation in product design, ultimately meeting the diverse needs of the market and enhancing competitiveness.
CNC Turning
CNC turning is a crucial aspect of CNC machining, where cylindrical parts are shaped and refined through precise cutting techniques. Utilizing tools that rotate the workpiece, this process allows for intricate designs that demand high-quality finishes. Entering CNC machining with a focus on turning can lead to the production of components that meet strict tolerances and specifications. Depending on the complexity of the design, 3-axis CNC machining may suffice, while more advanced configurations like 5-axis CNC machining are necessary for intricate geometries.
The demand for CNC machining services tailored to turning applications continues to grow across various industries. With expert CNC machining skills, suppliers can deliver high-precision CNC machining cuts that cater to specific client requirements. Multi-axis CNC machining offers greater flexibility in turning operations, enabling the creation of complex shapes and profiles that traditional methods may struggle to achieve. Engaging with capable CNC machining suppliers ensures a reliable production process and the quality assurance critical for successful projects.
Custom CNC Machining
CNC machining offers a tailored approach to fabricating parts, catering to unique specifications and requirements. By utilizing on-demand CNC machining, businesses can achieve rapid machining solutions that effectively reduce lead times. Skilled CNC machinists apply advanced CNC machining language to optimize the actual machining process, ensuring precision and quality in every project. This method not only enhances flexibility but also allows for the creation of complex machining parts that meet industry standards. Custom CNC machining stands out as a critical asset for industries seeking to innovate while maintaining cost efficiency.
Advantages of Custom CNC Machining
Custom CNC machining offers significant advantages over conventional machining methods by utilizing advanced computer-controlled machining technology. This precision-driven approach ensures that the machining process produces intricate custom machining parts with unparalleled accuracy. By leveraging sophisticated machining tools and techniques, manufacturers can execute complex designs that would be difficult or impossible to achieve through traditional machining processes. The ability to make rapid machining changes further enhances flexibility, allowing for quick adjustments during production.
Another key benefit of custom CNC machining is the efficiency gained throughout the machining steps. Automation minimizes human error and optimizes material usage, contributing to reduced waste. This efficiency leads to faster turnaround times compared to chemical machining and other less automated techniques. Custom CNC machining’s adaptability means it can cater to specific project needs, resulting in high-quality outputs tailored to various sectors and applications.
Applications of Custom CNC Machining
Custom CNC machining plays a crucial role across various industries due to its ability to meet specific machining requirements. This advanced form of computer-aided machining allows manufacturers to conduct complex machining operations with precision and repeatability. Unlike traditional machining or non-computerized machining methods, CNC machining integrates advanced technology into machining processes, significantly enhancing efficiency and accuracy.
The versatility of CNC machining makes it ideal for a wide range of applications. Industries such as aerospace, automotive, and medical rely on custom CNC machining to create tailored components that fit precise specifications. With the ability to streamline high-volume machining operations, companies can reduce production times and improve overall quality. This adaptability positions custom CNC machining as a vital component in the ever-evolving machining industry.
CNC Machining Equipment
CNC machining relies heavily on various types of equipment that play crucial roles in the execution of specific machining tasks. At the heart of the process are CNC milling tools and CNC machine tooling, which facilitate the manipulation of materials with precision. A machining table serves as a stable foundation for workpieces, ensuring accuracy during operation. Each CNC machine operates based on machining code, directing the movement of tools to achieve desired shapes and finishes. The choice of preferred machining method often influences the selection of equipment, as different tools cater to various basic machining processes. Ultimately, modern machining operations leverage advanced equipment to enhance efficiency and output quality, catering to the demands of diverse manufacturing environments.
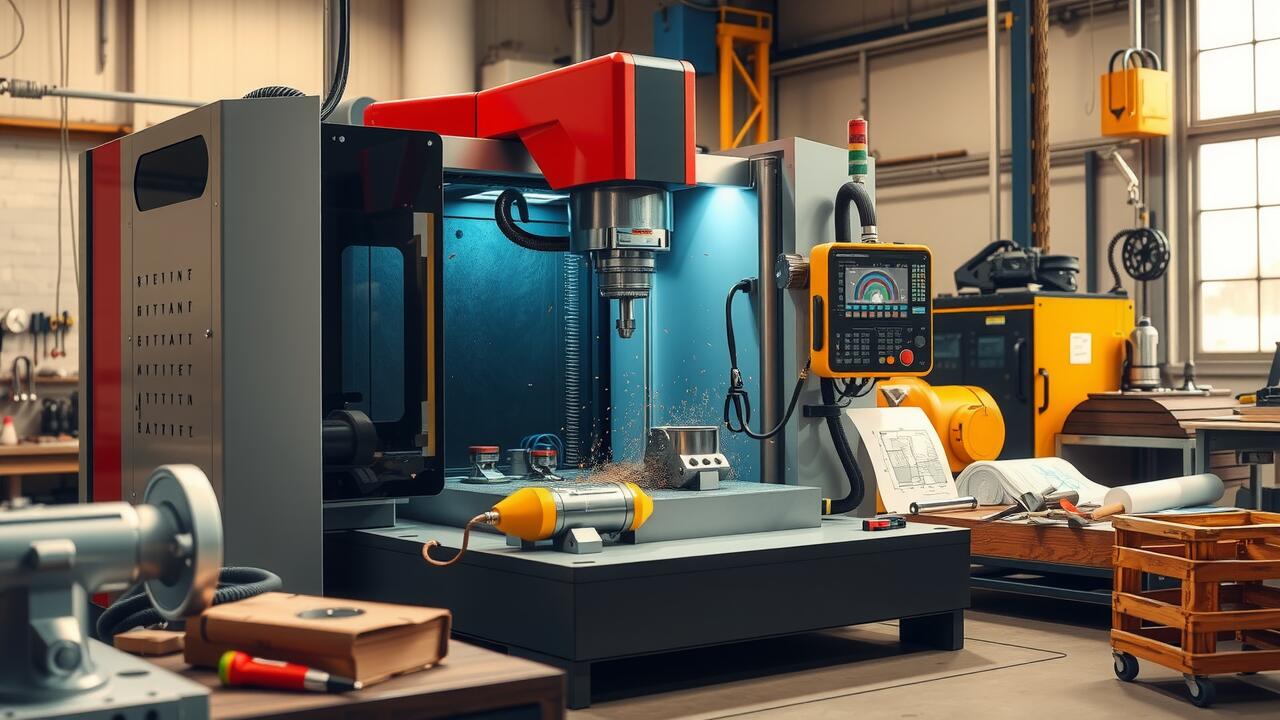
Essential CNC Machining Equipment
CNC machining relies heavily on specialized equipment designed to optimize machining efficiency. CNC-controlled machine tools form the backbone of the manufacturing process, enabling precise cuts and complex shapes. This equipment includes CNC mills, lathes, routers, and waterjet cutters, each facilitating efficient machining processes that enhance overall machining performance. The integration of computerized operation of machining tools used in manufacturing allows for automation and consistency, essential for high-quality output.
Training is crucial for CNC machinists to effectively use this sophisticated equipment. CNC machinist training helps operators understand the intricacies of various CNC machines, enabling them to maximize the capabilities of mechanical CNC systems. Well-trained machinists can leverage advanced CNC manufacturing techniques, ensuring that production runs smoothly and efficiently. Emphasizing the importance of proper equipment and skilled personnel strengthens the foundation of successful CNC machining operations.
Advanced CNC Machines
Modern CNC machines manufacture with precision and enhanced capabilities, making them essential for various manufacturing tasks. These advanced machines utilize sophisticated CNC tools that enable multi-axis CNC milling and various machining techniques such as Swiss machining. This versatility allows for efficient small-batch machining, reducing machining time while maintaining high quality. The integration of automation ensures that complex designs are produced with accuracy and consistency.
Post-machining evaluations are a critical aspect of ensuring quality in CNC machining processes. Advanced CNC machines are designed to accommodate a range of post-machining surface finishes, which can significantly enhance the final product's aesthetics and functionality. By leveraging technology and precision engineering, these machines enable manufacturers to achieve exceptional results across diverse applications, meeting the demands of a competitive market.
CNC Machining Materials
Understanding the materials used in CNC machining is crucial for optimizing the cnc fabrication process. Different materials, such as metals and plastics, exhibit unique properties that affect machining costs and overall efficiency. The cnc manufacturing application often requires careful selection of materials based on durability and machinability. For instance, CNC turning machines and CNC drilling processes perform differently depending on the material composition. Knowing how cnc machines work with various substrates allows manufacturers to tailor their approaches, ensuring high precision and quality in the final products. This knowledge enhances the effectiveness of the numerical control machining techniques employed in modern manufacturing environments.
Metals Suitable for CNC Machining
CNC machining offers versatility in working with various metals, enabling manufacturers to achieve high precision and quality. Commonly used metals include aluminum, steel, and titanium, all of which can be processed through techniques like 3-axis CNC milling and 5-axis CNC milling. These metals respond well to thermal machining processes and can be shaped effectively using many CNC tools. The CNC drilling process allows for the creation of intricate designs, making these metals ideal for components requiring tight tolerances.
Electrochemical machining processes also play a significant role in CNC machining of metals, particularly for complex geometries that are difficult to achieve through conventional methods. This process, along with traditional machining services order, allows for the effective removal of material without damaging the underlying metal. Whether it’s CNC metal fabrication or machining services, selecting the right metal is crucial for optimizing performance and durability in various applications.
Plastics in CNC Machining
CNC machining is increasingly popular for working with various plastics due to its versatility and precision. Modern CNC machines can handle a wide range of thermoplastics and thermosetting plastics, allowing manufacturers to produce intricate and detailed machinable parts. Basic CNC machines are often sufficient for straightforward tasks, while advanced CNC technology facilitates complex designs, ensuring high-quality results. Final finishing machining plays a critical role in achieving the desired surface texture and dimensional accuracy, which is crucial for functional plastic components.
The choice of CNC machine type greatly affects the efficiency and cost of CNC manufacturing services. Start-up machining costs can vary based on the complexity of the plastic part and the capabilities of the chosen CNC equipment. Selecting the right materials and machine setup leads to cost-effective solutions without compromising quality. Understanding the interplay between material properties and CNC machining techniques is essential for optimizing production in plastic applications.
CNC Machining Services
CNC machining encompasses a range of services utilizing standard CNC machines and advanced CNC-enabled machinery to produce various components. These services are essential for creating precision-engineered parts, from custom CNC parts tailored to specific requirements to larger CNC machines that handle bulk production. Different CNC machines, including CNC milling and multi-axis CNC machines, play a significant role in enhancing manufacturing efficiency. With the capability to produce intricate designs and high-quality finishes, CNC machining services cater to diverse industries, ensuring consistent results and meeting the demands for both small and large production runs.
Overview of CNC Machining Services
CNC machining services encompass a wide array of techniques and technologies designed to create precise components across various industries. Utilizing modern CNC technologies, these services often include the operation of global CNC machines such as three-axis CNC machines and advanced 5-axis CNC machines. Typical CNC parts produced through these processes can range from simple brackets to complex assemblies, each tailored to meet specific client specifications. The CNC process ensures high repeatability and accuracy, making it an essential resource for manufacturers.
Phenolic machining is one of the specialized services offered within CNC machining, effectively handling materials that require unique processing capabilities. Various CNC devices are employed to achieve optimal results, accommodating different materials and complexities. Clients seeking tailored solutions can benefit from the versatility of CNC machining services, ensuring that their projects receive the precision and attention to detail they demand. This adaptability makes CNC machining vital across sectors, enhancing production efficiency and product quality.
Selecting CNC Machining Suppliers
Choosing the right supplier for CNC machining can significantly impact the quality and efficiency of your projects. Look for manufacturers that specialize in various CNC operations, including CNC turning and indexed CNC milling. A reliable supplier should employ skilled CNC machine operators who are proficient in using advanced CNC systems. Their expertise ensures they can deliver precise CNC products tailored to your specifications, which is crucial for achieving successful outcomes.
Evaluating the capabilities of potential suppliers includes understanding the range of equipment they utilize, such as CNC plasma cutters, which can enhance the cutting process. Assess their experience with complex materials and intricate designs, as this will inform you about their ability to handle different demands. A strong track record in CNC machining services and positive customer testimonials are essential indicators of a supplier's reliability and expertise.
CNC Machining in Manufacturing
CNC machining plays a vital role in modern manufacturing, enabling precision and efficiency across various industries. The integration of CNC systems has transformed traditional manufacturing processes, with skilled machinists utilizing a dozen CNC machines to execute intricate designs and specifications. Different CNC operations, such as waterjet machining and electron beam machining, offer unique advantages for specific applications. Custom CNC solutions cater to diverse manufacturing needs, allowing businesses to produce tailored parts and components. Even hobbyists benefit from affordable hobby CNC tools, enhancing the accessibility of precision machining. As manufacturing continues to evolve, CNC machining remains a cornerstone of quality and innovation.
The Role of CNC Machining in Manufacturing
CNC machining has transformed the landscape of manufacturing, moving beyond the limitations of manual manufacturing. Skilled machinists leverage advanced CNC processes to create precision components quickly and with high accuracy. This technology enables a deeper machinability analysis, ensuring that the chosen materials, including additional CNC plastics, meet the requirements for specific applications. Each CNC machine’s remit allows for the production of complex geometries that would be challenging to achieve with traditional methods.
The basic CNC process utilizes computer-controlled machines to execute a variety of tasks, from milling to turning, resulting in high-quality CNC parts. This automation dramatically increases production efficiency and reduces the likelihood of human error. As manufacturers look to enhance their capabilities, CNC machining stands out for its versatility and precision, making it a cornerstone in modern industrial practices.
CNC Manufacturing Techniques
CNC machining has transformed manufacturing by enabling precision metal cutting with remarkable efficiency. Modern CNC systems utilize advanced CNC controls that enhance the accuracy of CNC programming works. These systems are designed to produce accurate CNC products, ensuring that each part meets stringent specifications. Basic CNC methods have evolved significantly, leading to more complex setups like mill-turning CNC centers, which combine milling and turning operations into a single process.
New CNC systems have introduced innovative techniques that enhance productivity and flexibility in manufacturing environments. These developments allow for intricate designs and high-volume production runs while maintaining consistent quality. Integrating sophisticated technologies with CNC machining optimizes workflow and reduces lead times, ultimately helping manufacturers meet the demands of a competitive market.
Efficiency in CNC Machining
CNC machining offers significant efficiencies through the use of advanced technologies like 3-axis CNC systems, which streamline production processes. This technology minimizes the need for manual machine tools, allowing for more precise and consistent outcomes. Operators benefit from resources such as the CNC programming handbook, which guides them in optimizing operations. The certification in CNC operations ensures that personnel are well-equipped to handle complex tasks, boosting productivity. With CNC-operated processes, manufacturers can achieve faster turnaround times, particularly in applications requiring a ft. CNC setup. By harnessing these efficiencies, businesses elevate their manufacturing capabilities significantly, leading to enhanced competitiveness in the market.
Quick-Turn CNC Machining
Rapid production is a hallmark of quick-turn CNC machining, catering to industries needing fast turnaround times for prototype and production parts. It streamlines the process using advanced 3-axis CNC milling and 5-axis CNC milling techniques to achieve precise geometry quickly. This efficiency allows for the integration of various machining services orders, facilitating swift responses to client requests. Many CNC tools, including those used in CNC drilling processes and thermal machining processes, enable manufacturers to produce components rapidly without sacrificing quality.
Quality control remains integral in quick-turn CNC machining to ensure that each part meets strict specifications. Electrochemical machining processes are often employed to achieve complex shapes with high precision. CNC metal components can be manufactured using these techniques, balancing speed and accuracy. With quick-turn capabilities, businesses can maintain competitiveness while addressing urgent demands in their manufacturing operations.
Online CNC Machining Solutions
The advent of online CNC machining solutions has transformed the way businesses approach manufacturing. Companies can now easily access various machining services online, allowing for streamlined orders and quick turnaround times. With options like 3-axis CNC milling and 5-axis CNC milling, users can find the precise machining capabilities they require. Many CNC tools are available for different applications, making it simple to choose the right equipment for specific projects. Thermal machining processes and electrochemical machining processes further expand the range of available techniques, catering to diverse industry needs.
Efficient CNC machining services are now just a click away, offering a comprehensive approach to metal and plastic processing. Customers can customize their machining services order to include CNC drilling processes, ensuring that they receive tailored solutions for their unique requirements. The flexibility of online platforms allows for easy adjustments and real-time tracking of projects, ensuring that deadlines are met without sacrificing quality. As the demand for CNC metal fabrication grows, embracing these online solutions will enable businesses to maintain a competitive edge in the marketplace.
Conclusion
CNC machining has become a cornerstone of modern manufacturing, revolutionizing the way components are produced with precision and speed. The CNC machining process allows for intricate designs and high tolerances, backed by a variety of CNC machining materials ranging from metals to plastics. Start-up CNC machining companies are leveraging instant CNC machining solutions, often turning to online CNC machining services to streamline operations and reduce lead times. As the CNC machining industry continues to evolve, the adoption of advanced CNC machining cutting techniques enhances efficiency and quality. Businesses can now access a wide array of CNC machining services tailored to specific needs, ensuring competitive advantage in a dynamic market.
FAQS
What is CNC machining?
CNC machining is a computer-controlled manufacturing process that uses pre-programmed software to dictate the movement of machinery and tools, allowing for high precision and automation in the production of parts.
What are the benefits of CNC machining?
The benefits of CNC machining include high accuracy, repeatability, reduced labor costs, the ability to produce complex shapes, and improved production speed, among others.
What types of CNC machining are available?
Common types of CNC machining include CNC milling, CNC turning, and custom CNC machining, each offering distinct processes tailored for various manufacturing needs.
What materials can be used in CNC machining?
CNC machining can work with a variety of materials, including metals such as aluminum, steel, and titanium, as well as plastics like acrylic, nylon, and polycarbonate.
How does custom CNC machining differ from standard CNC machining?
Custom CNC machining is tailored to meet specific design requirements and specifications, allowing for unique parts to be produced that may not be achievable through standard machining processes.
What advantages does CNC machining offer over traditional machining methods such as custom CNC milling and the use of CNC tools?
CNC machining, or computer numerical control (CNC) machining, offers several advantages over traditional machining methods. It enhances precision and consistency in the machining operation, which is vital for both metal CNC machining and plastic CNC machining. Additionally, CNC allows for efficient custom CNC milling, reducing the time required for production while maintaining high quality. The CNC manufacturing process also minimizes human error, resulting in better surface finishes and optimized machining operations, which would be challenging to achieve with traditional machining techniques. Moreover, with large CNC machines, the production capability is significantly increased, supporting both small and large-scale projects.
How can CNC machining be utilized in various machining operations, including metal CNC machining and plastic CNC machining, by a CNC machinist?
CNC machining, often referred to as computer numerical control (CNC), is essential in various machining operations, including processes like electric discharge machining and CNC riveting. A skilled CNC machinist can maximize the benefits of CNC machining by ensuring precise and efficient execution of tasks, whether it involves metal CNC machining, plastic CNC machining, or even operating specific machinery covered under CNC certification, all of which fall within the CNC machine's remit.
How does cnc machining influence the quality of cnc machining surface in modern manufacturing processes?
The quality of the cnc machining surface is significantly enhanced in modern manufacturing processes due to the precision and consistency offered by cnc (computer numerical control) techniques. As a result, cnc machining has become integral to various machining operations, including cnc milling and others, which fall within the cnc machine's remit.
How does cnc machining improve efficiency in various industrial applications compared to traditional machining techniques?
CNC machining significantly enhances efficiency within a CNC machinist's remit by automating processes that were previously done manually. This advancement allows for faster production cycles and consistent quality in outputs, which is crucial for tasks like CNC milling and other machining applications. As a result, industries see increased productivity and reduced waste in their machining operations.
How does the integration of advanced technologies impact cnc machining and its applications in the field of cnc?
The integration of advanced technologies significantly enhances cnc machining by improving precision and automation. This allows for greater efficiency in applications such as cnc millingâ andâ optimizes the cnc machineâs remit, making processes smoother and more consistent in various manufacturing settings.
How does the evolution of cnc machining influence CNC processes in the modern manufacturing landscape?
The evolution of cnc machining significantly enhances CNC processes by integrating state-of-the-art technology, which improves both efficiency and precision in machiningâ. This advancement allows for more complex designs and high-quality output in various applications, ultimately transforming the field of cnc machiningâ.
How does the implementation of new technologies enhance cnc machining and its relevance in the field of cnc?
The implementation of new technologies significantly enhances cnc machining by introducing innovations that improve efficiency, accuracy, and versatility in manufacturing processes. These advancements allow for the integration of enhanced features and functionalities into cnc machining systems, making them vital in the evolution of modern cnc techniques and applications in various industrial sectors.
How does the future of cnc machining influence advancements in the cnc industry?
The future of cnc machining is set to significantly influence advancements in the cnc industry by incorporating new technologies that enhance efficiency, precision, and automation. As we enter an era of smart manufacturing, cnc machining will play a critical role in driving innovation and improving overall operational effectiveness in various industrial applications.
How does CNC machining optimize the production process in various industries using advanced CNC technologies?
CNC machining enhances the production process by increasing precision and efficiency, allowing for greater flexibility in design and reducing waste. When utilizing advanced CNC technologies, manufacturers can streamline operations, resulting in cost-effective solutions that cater to the specific needs of various industries such as automotive and aerospace, ensuring that CNC machining remains relevant in modern manufacturing practices.
How is the role of CNC machining evolving in the context of innovations in CNC technology?
The role of CNC machining is evolving significantly as new CNC technologies are introduced, enhancing the precision and capabilities of CNC machining. These advancements help improve the efficiency of various industrial applications, allowing for more complex designs and higher production rates. The integration of innovative tools and processes is crucial for maintaining competitiveness in the CNC industry.