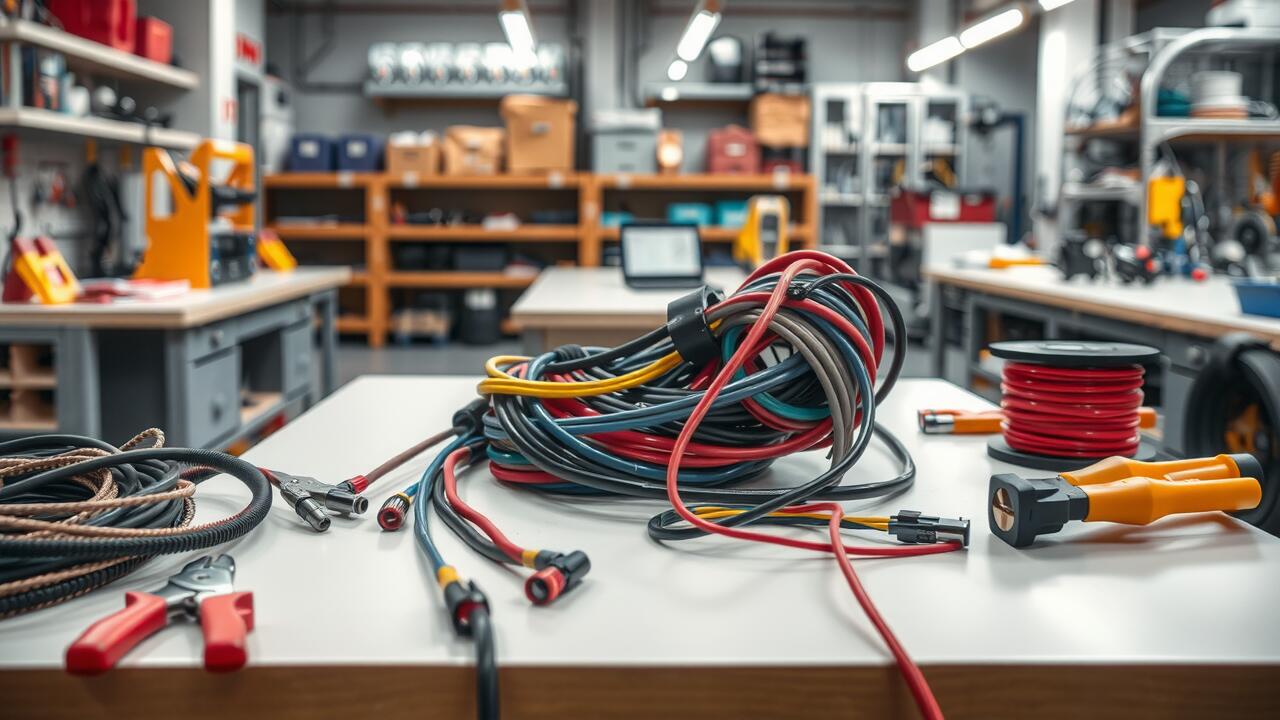
Key Takeaways
- Summary of Custom Wiring Assemblies and Their Varieties
- Insights into Crafting Tailored Electrical Networks
- Overview of the Production Approach for Wire Assemblies
- Guidelines for Choosing a Wire Assembly Producer
- Uses of Tailored Electrical Harnesses in Various Industries
- Benefits of Personalized Wire Assemblies in Manufacturing
Overview of Custom Wire Harnesses
Custom wire harnesses play a vital role in various industries by streamlining the connection and organization of electrical components. A wire harness, composed of wires and cables, provides a structured way to transmit power and signals, enhancing the safety and reliability of electronic systems. These wiring harnesses are tailored for specific applications, ensuring that the unique requirements of each project are met effectively. Custom wire harness solutions can include various features such as specialized power cords and connectors, which help to optimize performance and reduce installation time. With the right design and manufacturing processes, custom wire harnesses significantly enhance the overall functionality of many electronic devices and systems.
Definition of Wire Harnesses
A Custom Wire Harness is an assembly of multiple wires and connectors designed to transmit electrical power and signals between different components of a device or machine. It consists of a multi conductor cable insulated to prevent electrical shorts, ensuring reliability in various applications. Often, these wire harnesses are tailored to specific requirements, allowing for seamless plugging in and connecting multiple devices efficiently, such as power cords that connect to power sources.
The design of a wire harness plays a crucial role in the overall functionality of electrical systems. Proper insulation and the right choice of connectors are essential to maintain an effective supply chain of electrical signals. Custom Wire Harnesses provide a streamlined approach to integrating power and data connections, offering solutions that fit unique operational needs. Each assembly is crafted to minimize interference and optimize performance, making them indispensable in industries ranging from automotive to consumer electronics.
Importance of Custom Manufacturing
Custom wire harness manufacturing plays a crucial role in the development of complex electrical systems. These harnesses are designed to connect various components, such as plugs and connectors, ensuring efficient transmission of electrical signals. With a tailored approach, manufacturers can incorporate specific elements like voltage regulators and electromechanical devices to meet the unique requirements of different electronics applications.
The significance of custom manufacturing lies in its ability to provide solutions that enhance performance and reliability. By utilizing specialized materials and precise designs, custom wire harnesses can withstand varied voltage levels and environmental conditions. This customization not only improves functionality but also reduces the risk of failure in critical systems, making it essential for industries reliant on sophisticated electrical infrastructure.
Types of Custom Wire Harnesses
Custom Wire Harnesses come in various types, each designed to meet specific needs across different industries. Automotive Wire Harnesses are essential for connecting critical components such as the fuse box, socket, and switch, ensuring seamless vehicle operation. Engine Wiring Harnesses focus on the intricate network required for managing power delivery and sensor signals, incorporating elements like relays and fuses. Industrial Wiring Harnesses cater to heavier machinery and equipment, often including features such as plug and play connectors for efficient setup and maintenance. Some harnesses are designed for specialized applications, such as those involving trailer hitches, where precise wiring is crucial for safety and functionality. Each type is meticulously crafted to ensure optimal performance and reliability.
Automotive Wire Harnesses
Custom Wire Harnesses play a critical role in the automotive industry, ensuring vehicles operate efficiently and safely. These harnesses are designed to connect various components, such as the engine and battery, using specific configurations of pins and plugs. The plug-and-play feature enhances ease of installation, allowing for straightforward connections to systems like tail lights and alternators, which are vital for vehicle functionality.
A well-thought-out design is essential for automotive applications, particularly in complex systems like trailers and engine layouts. Custom Wire Harnesses can be tailored to meet unique requirements, providing solutions that cater to different vehicle types and specifications. By focusing on durability and adaptability, manufacturers ensure that the wire harnesses can withstand the rigors of automotive environments while maintaining seamless operation across multiple systems.
Engine Wiring Harnesses
Engine wiring harnesses play a critical role in the operation of a vehicle’s engine management system. These custom wire harnesses are designed to meet specific engine specifications, ensuring optimal performance and reliability. For vehicles such as the Tacoma, the entire wire harness must cater to various electronic components, including sensors and actuators. By utilizing a custom wire harness, manufacturers can streamline installation and improve the overall efficiency of the engine's functionalities.
The design of a custom wire harness tailored for engine applications often includes a variety of connectors and protective features. These components are essential to managing electrical connections while safeguarding against environmental factors. The next wire harness created for engine systems will focus on enhancing durability and performance while adhering to safety regulations. Custom wire harnesses thus provide solutions that meet the unique demands of engine wiring, supporting both functionality and innovation.
Industrial Wiring Harnesses
Industrial wire harnesses play a crucial role in various sectors, ensuring the reliable transmission of power and data. A custom wire harness tailored to specific industrial applications can significantly enhance operational efficiency. These high-quality wire harness products are designed to withstand harsh environments and rigorous demands. Custom wiring harness solutions can improve the longevity and reliability of equipment. Companies often seek quality wire harnesses to ensure their industrial systems operate seamlessly.
Custom wire harness manufacturing processes focus on creating wire harness assemblies that meet stringent industry standards. By utilizing advanced technologies, manufacturers can produce industrial wire harnesses that cater to diverse applications. These wire harness products often require specialized components to optimize performance. Industries that rely on automotive wire harnesses can also benefit from the precision and customization available in industrial wire harness production. A commitment to quality in wire harness manufacturing is essential for both safety and performance in industrial settings.
Designing Custom Wiring Harnesses
Creating a new wiring harness involves a thorough understanding of the specific requirements for the application at hand. Each custom wire harness must be designed to accommodate the unique features of the equipment it will serve. This process includes evaluating the dimensions, load capacity, and environmental factors that could impact performance. The wire harness assembly should incorporate advanced wiring harness technologies to ensure reliability and efficiency. Features such as customizable lengths, connector types, and shielding options make it possible to create an ideal custom wire solution that meets the demands of various industries. A well-planned design will yield harness custom tailored to provide optimal functionality and durability across diverse applications.
Assessing Wiring Harness Requirements
Understanding the specific requirements for a Custom Wire Harness is essential for effective design and functionality. Factors such as the intended application, environmental conditions, and space constraints play a crucial role in determining the specifications. Automotive wiring harnesses, for example, require robust designs to withstand vibrations and heat, while a pre-wired harness for consumer electronics might prioritize compactness and flexibility. Collaborating with a manufacturer custom wire that specializes in these areas ensures that the wiring harness wiring meets all necessary regulations and standards.
Identifying the critical components of a cable harnesses is vital for achieving a successful outcome in custom harness form. For engine wiring harness applications, the selection of materials must align with the specific requirements for durability and performance. Custom wire industries often provide diverse options for insulation, connectors, and terminals, allowing manufacturers to create tailored solutions that cater to unique technological demands. Comprehensive assessment of these elements guarantees optimal performance and reliability in the final product.
Key Components of a Custom Wire Harness
A Custom Wire Harness typically consists of several essential components that ensure its functionality and reliability. These components include various wire types, connectors, terminals, and protective coverings. High-speed custom wire is often chosen for applications requiring rapid data transmission. Quality custom wire ensures durability and resistance to environmental factors, while trusted custom wire manufacturers focus on providing products tailored to specific operational needs, such as engine wiring harnesses.
The design of a reliable Custom Wire Harness also involves considering the assembly layout and securing methods for the components. Computerized wiring harness systems can optimize the harness structure for improved efficiency and performance. Top-quality custom wire options are crucial for maintaining signal integrity and minimizing potential interference. By selecting the right materials and components, manufacturers create harnesses that meet the demands of various industries, ensuring that every aspect of the wiring solution is meticulously crafted.
Customizable Wiring Harness Features
The versatility of a Custom Wire Harness allows for an extensive range of harness options tailored to meet specific project requirements. A reliable harness manufacturer will work closely with the custom wire team to develop solutions that enhance functionality and efficiency. From simple harnesses to more complex arrangements, the ability to customize each component ensures that the final product aligns perfectly with the intended application. This adaptability is crucial across various wire industries, where unique needs dictate the specifications of the harness.
Functional wire plays a significant role in the overall design of a custom harness, impacting both performance and reliability. Manufacturers often provide comprehensive consultations to evaluate the needs of their clients, allowing for the creation of a comp custom harness that meets all specifications. The focus is not only on the physical attributes but also on how these harnesses can be integrated seamlessly into existing systems. By considering factors like size, weight, and environmental conditions, the custom wire team ensures that every aspect is optimized for the best user experience.
Wire Harness Manufacturing Process
The manufacturing process of custom wire harnesses involves several critical stages that ensure the production of high-quality harnesses tailored to specific requirements. Harness manufacturers begin by assessing wire specifications and determining the necessary wire identification for each application. This careful planning is essential for creating complex harness systems that meet industry standards. Utilizing superior wire materials, manufacturers can produce durable and reliable automobile wire harnesses that perform optimally under various conditions. As a result, businesses benefit from customized harness solutions designed to fit their needs precisely, enhancing overall functionality and reliability in their products.

Stages of Wire Harness Assembly
The wire construction process for a Custom Wire Harness involves several carefully orchestrated stages. Initial steps include the detailed design and layout of harness assemblies that prioritize efficiency and safety. During assembly, loose wires must be meticulously organized to prevent any interference, ensuring that the final product meets the necessary specifications. This is particularly crucial for complex systems such as an engine harness, where the harness transmits power to various components.
Following the initial assembly, the focus shifts to integrating a rigid harness design that enhances durability. Quality checks are critical at this juncture, ensuring that any faulty connections from old harness systems are identified and rectified. Every stage emphasizes precision in the wiring to guarantee optimal performance and reliability, making every Custom Wire Harness an essential part of modern machinery and automotive design.
Materials Used in Wire Harness Production
The selection of materials for Custom Wire Harness production is critical to ensure optimal performance and durability. High-quality electromechanical wires are often utilized due to their excellent conductivity and flexibility. Custom power cords also play a vital role, providing tailored solutions for various applications. Wire assemblies are designed using these materials to withstand cable wear, while shrink wire may be used for insulation, enhancing safety and reliability. Incorporating effective wire markings facilitates easier identification and installation in complex projects.
Aerospace wire is another specialized material used in Custom Wire Harnesses, ensuring that products meet stringent industry standards. This type of wire is designed to endure harsh environments, contributing to consistent harness performance in critical applications. Manufacturers focus on utilizing a combination of materials to optimize both functionality and longevity. The integration of various components in the assembly process is crucial, allowing for a reliable and efficient final product that excels across diverse industries.
Quality Control in Wire Harness Manufacturing
Quality assurance is critical in the production of Custom Wire Harnesses. Each stage of the harness assembly process requires rigorous checks to ensure that all cable types and cords meet specified standards. From the initial selection of materials to the final inspection, every detail is scrutinized. This ensures that electromechanical device wiring is executed flawlessly and meets technical cable applications' requirements. Correct harness sequence and compliance with cable tooling requirements are paramount to achieving high-quality outcomes.
Testing procedures play a vital role in maintaining the integrity of cable products used in Custom Wire Harnesses. Manufacturers implement thorough evaluations to examine the performance and reliability of each harness. Elements such as resistance to environmental factors and operational efficiency are reviewed for assurance. By adhering to strict quality control protocols, companies can guarantee that their Custom Wire Harnesses will perform optimally in their designated applications, minimizing the risk of failure and maximizing customer satisfaction.
Selecting a Wire Harness Manufacturer
Choosing the right manufacturer for a Custom Wire Harness involves careful consideration of various factors to ensure quality and reliability. A reputable manufacturer should demonstrate expertise in wire assembly, showcasing advanced cable capabilities that can accommodate diverse applications. Look for options that offer specialized features such as wire armor splits for enhanced protection and durability. Equally important is the ability to handle standard trailer wiring alongside more complex current performance wiring needs. Manufacturers offering custom cord solutions enable tailored designs that meet specific requirements, making them highly valuable in any project involving wiring. Selecting a partner who understands your unique demands will help streamline production and ensure optimal functionality.
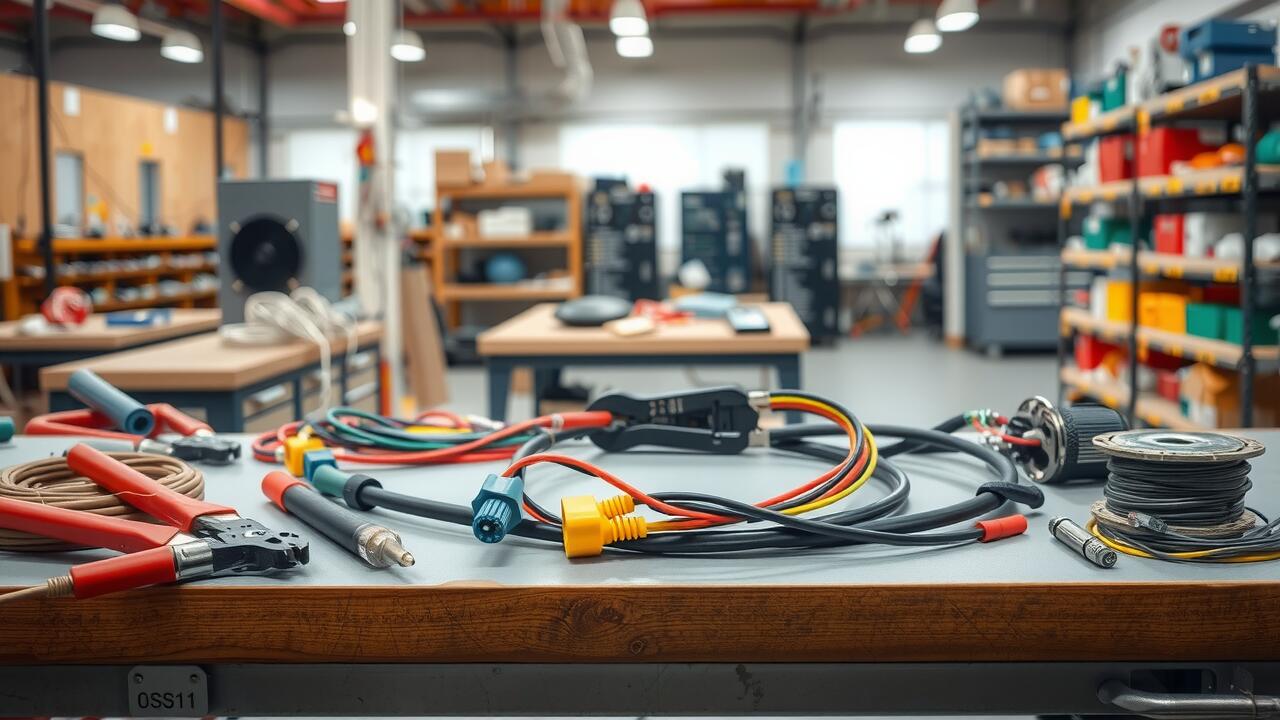
Factors to Consider When Choosing a Manufacturer
Selecting the right manufacturer for your Custom Wire Harness is crucial for achieving an effective wiring solution. Quality craftsmanship can significantly reduce the occurrence of unnecessary wiring, leading to improved reliability and performance. A manufacturer that specializes in custom cord production and cable assemblies will have the expertise to create tailored solutions that fit your specific requirements. Whether you're working on complex projects like a single-wire alternator or straightforward applications such as radio wiring, choosing a knowledgeable partner ensures the final product meets industry standards.
Another essential factor is the capabilities of the manufacturer in terms of cable fabrication services and the availability of skilled wiring assemblers. A strong portfolio of past projects can be indicative of their proficiency in handling various wiring needs. Communication is key; manufacturers that maintain open lines can help in refining specifications and addressing concerns promptly. By evaluating these factors, you can establish a solid partnership that enhances your Custom Wire Harness project, ensuring it meets both quality and performance expectations.
Top Wire Harness Manufacturers in the Industry
Leading manufacturers of Custom Wire Harnesses specialize in delivering high-quality solutions tailored for a wide range of applications. These companies excel in producing cable assemblies that meet the exact specifications of various electrical devices, ensuring compatibility and functionality. Their expertise extends to complex engine wiring, where they design custom connectors that facilitate seamless connections. The choice of insulation style plays a crucial role in safeguarding the electrical supply, making it vital for manufacturers to prioritize materials that enhance durability and performance.
Many top manufacturers are also known for their commitment to innovation, offering advanced options for custom wire harnesses that integrate efficiently into electromechanical devices. They understand the importance of producing a reliable cord that withstands demanding environments. With their extensive knowledge in cable assembly techniques, these manufacturers ensure that every harness is meticulously crafted to meet stringent industry standards. By focusing on quality and customization, they play a key role in enhancing the performance of various applications across different sectors.
Custom Wire Industries and Their Offerings
Custom wire industries specialize in the production of Custom Wire Harnesses that cater to various applications, ensuring reliable connection and functionality for different equipment. They often collaborate with connector manufacturers to create tailored solutions, which include components like door lock relays and weatherproof connectors. Advanced techniques such as connector tooling and electrical testing are employed to ensure quality and durability, providing clients with peace of mind regarding their harnesses' performance.
The offerings from these industries extend to a broad range of applications, including automotive and industrial uses. For instance, Custom Wire Harnesses designed for trailer hitch receivers incorporate robust pin connectors that withstand harsh environments. Companies prioritize the development of harnesses that not only meet performance standards but also enhance safety and efficiency in their respective fields.
Applications of Custom Wire Harnesses
Custom wire harnesses play a crucial role across various industries, providing tailored solutions that meet specific application needs. In the automotive sector, these harnesses connect critical electromechanical components with precision, ensuring efficient power distribution and data transmission. Industrial applications often utilize rigid bundles that streamline wiring for automated equipment, enhancing reliability and ease of maintenance. Consumer electronics rely on custom wire harnesses featuring plug-and-play connectors, which simplify installation and facilitate repairs. By ensuring conductors are neatly organized and connectors remain clean, manufacturers can achieve optimal performance in diverse electromechanical applications, reinforcing the significance of custom wire harness solutions across multiple fields.
Automotive Industry Applications
Custom Wire Harness solutions play a vital role in the automotive industry by ensuring seamless connectivity between various electronic devices. One notable component is the curt easy-mount connector, which simplifies installation and maintenance processes. This ease of use is critical in modern vehicles, where a new plug can often be integrated with solar panel wire systems to enhance energy efficiency. Manufacturers often utilize bundles of wires wrapped with tape to meet the specific requirements of original equipment, delivering reliability and efficiency.
The demand for Custom Wire Harnesses in automotive applications extends beyond just connectivity. These harnesses are designed to withstand the rigors of different environments, providing durable solutions for various devices within the vehicle. Whether connecting sensors, lights, or infotainment systems, a well-designed Custom Wire Harness ensures optimal performance. The strategic arrangement of wires in these bundles not only minimizes space but also enhances the overall aesthetic of the automotive design, proving essential for integrating advanced technology in vehicles.
Aerospace and Defense Applications
Custom Wire Harness solutions play a crucial role in the aerospace and defense sectors due to their ability to ensure high electrical performance in complex systems. These harnesses often utilize specialized components such as flat sockets and t-connectors, which enhance connectivity while also promoting safety in various applications. The precise design features contribute to reducing the risk of electrical fires, which can be catastrophic in these high-stakes environments.
The connector development process for aerospace and defense applications demands rigorous testing and compliance with strict industry standards. Custom Wire Harnesses not only facilitate efficient connections between critical components but also streamline repairs and maintenance, ensuring reliability over the life span of the equipment. Features like hitches provide added support and durability, making them indispensable for mission-critical systems where failure is not an option.
Consumer Electronics Applications
The demand for advanced technology in consumer electronics has led to the increased use of Custom Wire Harness solutions. A well-designed Custom Wire Harness is crucial for efficient operation, particularly within devices such as audio equipment, gaming consoles, and home automation systems. Starting with a high-quality fuse box, these harnesses often incorporate tubes to protect wiring, ensuring durability throughout their use. OEM-compatible connectors improve compatibility with existing systems, while gauges help monitor performance effectively.
For consumer electronics, Custom Wire Harnesses can also streamline connections between components like control panels and dual battery switches. Each harness is tailored to meet specific requirements, allowing manufacturers to optimize their products’ functionality and reliability. Tooling techniques play a significant role in the production process, ensuring that each wire is securely connected in the chain of operation. This attention to detail promotes efficiency and enhances user experience across a broad range of electronic devices.
Advantages of Custom Manufactured Wire Harnesses
Custom Wire Harnesses provide tailored solutions that cater directly to the unique requirements of various industries, including automotive and aerospace. For example, in the automotive sector, a Custom Wire Harness can integrate components like an alternator voltage regulator and fuel injector, ensuring optimal performance of the vehicle's electrical systems. In complex machinery, such as robotic and processing equipment, these harnesses facilitate reliable connections and supply power efficiently. The inclusion of high-quality fuse boxes within these assemblies enhances safety and functionality, making them essential for military equipment and advanced technology facilities. Custom Wire Harnesses not only streamline production but also elevate product reliability in demanding applications.
Tailored Solutions for Specific Needs
Custom Wire Harness solutions are designed to meet the unique requirements of various applications. By leveraging a plug-and-play design, these harnesses provide ease of installation and flexibility for users. Custom Wire Harness manufacturing allows for adaptations that align with specific project needs, ensuring optimal performance and reliability.
The benefits of a Custom Wire Harness extend beyond mere functionality. They offer enhanced organization of electrical systems, reducing clutter and potential hazards. By utilizing a tailored approach, manufacturers can incorporate specific features such as enhanced insulation or specialized connectors, further enhancing the overall efficacy of the Custom Wire Harness.
Conclusion
Custom Wire Harnesses play a pivotal role in the functionality of various electrical devices and systems. These harnesses ensure reliable electrical supply by organizing complex engine wiring and providing essential connections through custom connectors. Each cable assembly is meticulously designed to suit specific requirements, incorporating diverse insulation styles and cord configurations. The versatility of Custom Wire Harnesses extends across multiple industries, making them indispensable for electromechanical devices and applications that demand precision and efficiency. Selecting the right harness ultimately impacts the performance and longevity of the electrical systems in which they are integrated.
FAQS
What is a custom wire harness?
A custom wire harness is a collection of wires and connectors designed and manufactured to meet specific requirements for a particular application, ensuring optimal performance and functionality.
Why is custom manufacturing important for wire harnesses?
Custom manufacturing allows for tailored solutions that meet the unique electrical and environmental demands of specific applications, enhancing reliability and efficiency.
What are the different types of custom wire harnesses?
The types of custom wire harnesses include automotive wire harnesses, engine wiring harnesses, industrial wiring harnesses, and more, each designed for specific industries and applications.
How do I assess my wiring harness requirements?
Assessing wiring harness requirements involves evaluating factors such as electrical load, environmental conditions, space constraints, and any specific connector or wiring needs for your application.
What are the key components of a custom wire harness?
Key components include wires, connectors, terminals, shielding, and insulation materials, all of which work together to ensure effective electrical transmission and protection.
What materials are commonly used in wire harness production?
Common materials include copper or aluminum for wires, various types of insulation (like PVC or silicone), and durable outer sheathing materials for protection against environmental factors.
How does the manufacturing process of wire harnesses work?
The manufacturing process typically involves designing the harness, sourcing materials, cutting and stripping wires, assembling components, and conducting quality control checks before final delivery.
What should I consider when selecting a wire harness manufacturer?
Consider factors such as the manufacturer’s experience, capabilities, certifications, quality control processes, and their ability to meet your specific project timelines and requirements.
What are the advantages of custom manufactured wire harnesses?
Advantages include optimized performance for specific applications, improved reliability, reduced installation time, and the ability to address unique design challenges effectively.
In which industries are custom wire harnesses commonly used?
Custom wire harnesses are widely used in industries such as automotive, aerospace and defense, consumer electronics, industrial machinery, and medical equipment.
What are the benefits of using customizable wiring harnesses in your projects, especially when ensuring that each harness part is tailored to specific needs?
Utilizing customizable wiring harnesses allows you to create a custom harness custom-made for your application, ensuring that every component, such as a connector clean and contact custom cord, perfectly fits your needs. These harnesses can connect various devices seamlessly and start with a high-quality fuse box, making them ideal for complex systems like robotic equipment commonly found in facilities.
How does a custom wire harness facilitate the process of connecting components, ensuring that each plug-in is suited to the needs of the facility?
A custom wire harness is designed to efficiently connect various components within a facility, enabling seamless plug-in capabilities. By tailoring each aspect of the harness to specific requirements, it ensures that all connections are reliable and suit the operational demands of the facility, improving overall functionality.
How can a custom wire harness improve the efficiency of how components plug in and connects within a system?
A custom wire harness greatly enhances system efficiency by ensuring that each component seamlessly plugs in and connects as intended. This tailored approach minimizes errors and optimizes space, allowing components to interface effectively in any given application.
How does the design of a custom wire harness impact the way components plug in to a system?
The design of a custom wire harness significantly impacts how components plug in by ensuring that each connection is specifically tailored to fit the requirements of the system. This customization helps reduce errors during installation and improves the overall efficiency of connections, making the process smoother and more reliable.
What factors should you consider when choosing a custom wire harness for your project?
When selecting a custom wire harness, you should consider the specific requirements of your project, including the types of components you need to connect, the environment in which the harness will operate, and the necessary customization for efficient connections. Additionally, ensure that the design and materials chosen complement the overall functionality of the system.